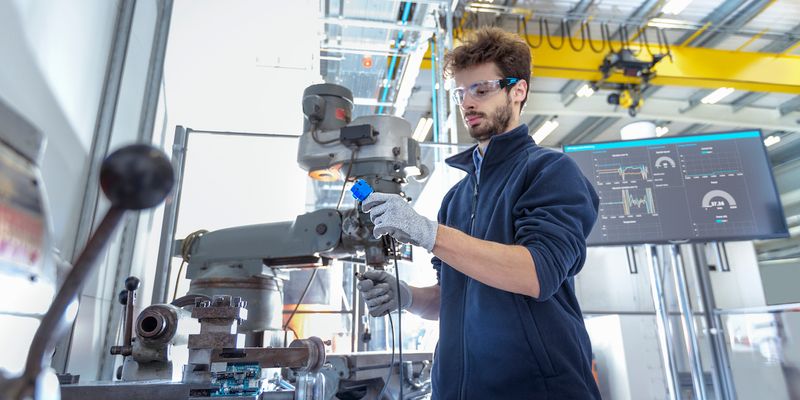
Grâce au kaizen, les personnes ont l’opportunité de participer directement à l'amélioration. Mais sans un suivi et une responsabilité claire d’un manager, ils se retrouveront seuls face aux conséquences des changements introduits. Un article de Eivind Reke, Cyril Gras et Daryl Powell.
Changer pour le meilleur, sacrifice personnel, amélioration continue. L’art du kaizen peut être interprété de différentes manières. Et si c’était encore plus simple que cela ? Chaque fois que nous parlons de lean avec nos amis Japonais, ils sont toujours aussi fascinés par nos interprétations si élaborées des mots et concepts. Par exemple, saviez-vous que les kanji dans le mot kanban se traduisent en « regardez de près le panneau de bois »? Ou que le kai de kaizen se traduit par « se fouetter »? « Très intéressant » et « très intelligent, trop intelligent pour moi » sont des remarques que nous entendons habituellement lorsque nous nous laissons aller à notre prédilection pour la sur-interprétation et la sur-analyse de ce que nous ne comprenons pas. Nous sommes tout aussi coupables que n’importe qui d’autre, nous ne blâmons personne: nous sommes tous en train d’essayer de comprendre cette chose qu’est le lean. Et si nous prenions un peu de recul et réfléchissions de nouveau à la situation?
Quel est l’unique élément du kaizen qui le distingue des autres méthodes et concepts d’amélioration ?
SORTIR DE LA LOGIQUE D'AMÉLIORATIONS ALÉATOIRES, CHERCHER À MIEUX FAIRE LES BONNES CHOSES
Commençons par une histoire. Deux d’entre nous, Eivind et Daryl, visitions ensemble une entreprise avec Michael Ballé dans le cadre de notre tour annuel de gemba en Norvège. Cette entreprise avait embauché un pratiquant du lean en tant que manager du système de production et, comme tout bon gars lean, il s’est attelé à la réalisation d’améliorations, en impliquant les opérateurs et en rendant le flux visuel. Lors de la visite, il nous a montré quelques-unes des améliorations dont il était particulièrement fier, ayant retiré des activités inutiles des opérations manuelles dans la production d’un des nouveaux produits de l’entreprise. Ils avaient fait plein de choses, de la réalisation de kitting de pièces à l’équilibrage des tâches entre les stations de travail en passant par le rapprochement des pièces de la ligne. Cependant, Michael sentait qu’ils ne s’étaient pas attelés au vrai sujet – et après que le manager lean eut poussé les opérateurs à participer à la discussion, celle-ci convergea vers les changements d’ingénierie qui avait été faits sur le produit. Ces changements avaient amené certains produits à être expédiés avec un défaut qui semblait bénin, mais était en fait sérieux – un défaut qui pourrait avoir de sérieuses répercussions sur le client. Plusieurs mois plus tard, le manager lean nous a révélé qu’après le gemba, lui et les opérateurs se sont attaqués à cette problématique et ont trouvé un moyen de corriger le défaut par du kaizen.
Mais pourquoi ne l’avaient-ils pas traité dès le début ? Et qu’est-ce que cela signifie pour notre compréhension du kaizen ?
Quand bien même nous pouvons et probablement devrions faire du kaizen pour supprimer les muri, mura et muda du processus, le gros gain qu’il apporte réside dans les changements d’ingénierie et leur suivi. Premièrement, le lean manager a travaillé sur le problème qui lui semblait être le plus important, retirer de la variation du processus. Pourtant, Michael y a vu un autre type de variation: une variation d’ingénierie qui provenait des changements d’ingénierie qui avait été faits sur le nouveau design du produit, que les opérateurs ont dû gérer par eux-mêmes alors qu’ils n’avaient aucun moyen d’en assurer le suivi, avec pour conséquence des produits qui se retrouvaient parfois bons, parfois mauvais. Au bout du compte, le problème s’est avéré être un manque de connaissance des paramètres techniques parmi certains opérateurs, ce qui a abouti à la réalisation de produits hors des tolérances d’ingénierie, et in fine des défauts. Une fois que la cause racine fut identifiée et comprise, les opérateurs eux-mêmes ont développé un standard de travail avec des instructions très claires, étape par étape, la raison de chaque étape, et les points de connaissance critiques.
LIVRAISON À DOMICILE
Il y a maintenant une éternité, en 2016, Aramis Auto a décidé de réaliser un grand changement dans leur offre produit, qui allait requérir un gros effort d’ingénierie de leurs opérations logistiques mais aussi administratives, financières, ainsi que dans le marketing et la conception de l’offre. Ils ont voulu introduire la livraison à domicile des voitures achetées par leurs clients en ligne. Le but était d’améliorer progressivement les ventes dans les zones de France qui, à cette époque, se trouvaient loin de leurs points de vente. Le processus a été développé par une équipe de managers qui avaient besoin de se mettre d’accord sur la façon de le faire fonctionner en équipe. Comme toujours avec de nouveaux processus, les choses ne fonctionnaient pas comme prévu. Les livraisons étaient en retard, les délais longs, et les clients insatisfaits. Pendant un long moment, les personnes dans le processus, furent laissés seules face aux problèmes et aux conséquences de ce grand changement. Cependant, Juliette, une ancienne kaizen officer, arriva pour prendre le rôle opérationnel. Elle commença par faire un vrai suivi. Grâce au kanban, elle fut capable d’identifier de petits problèmes un à la fois, et elle commença à les résoudre avec son équipe et à construire de nouvelles façons de travailler qui ont finalement abouti à des livraisons à l’heure, des délais plus courts et des clients satisfaits.
LE KAIZEN C’EST LES CHANGEMENTS D'INGÉNIERIE ET LEUR SUIVI
Assez curieusement, les trois livres de la trilogie The Goldmine de Michael Ballé traitent tous de la façon dont des personnes se développent en gérant des changements d’ingénierie qui, d’une façon ou d’une autre, ont eu pour résultat des produits de mauvaise qualité, de la surcharge et des processus inefficaces. Dans Le Gold Mine, Phil se démène pour réussir à introduire le nouveau produit dans les processus de production existants. Dans The Lean Manager, Andrew doit faire en sorte que son usine soit profitable en introduisant de nouveaux produits tout en réduisant le coût des produits existants. Enfin, dans Lead with Respect, Jane doit trouver un moyen de faire évoluer le logiciel d’une solution unique à une solution plus flexible qui puisse soutenir l’activité du client et non l’obliger à se conformer au système informatique. La question est donc: pourquoi est-il si compliqué d’emprunter cette voie de l’ingénierie lorsque nous faisons du kaizen ?
Le Lean n'est pas né en Europe ou aux États-Unis. Certes, ce sont des ingénieurs allemands qui ont transmis le concept du « takt-time » aux ingénieurs japonais. Certes, Kiichiro Toyoda a été inspiré lors d'une visite aux États-Unis par la chaîne d’assemblage en flux continu mise au point par Henry Ford. Et certes, Toyota a découvert le programme TWI après la guerre et a été inspiré par les célèbres conférences de Deming au Japon. Toutefois, attribuer l'origine du lean à l'un de ces événements serait comparable à la célèbre scène du film La vie de Brian des Monty Python, dans laquelle Brian se débarrasse enfin de ses disciples indésirables, mais perd une sandale au passage. Chacun dans la foule se met alors immédiatement à interpréter l'événement à sa manière, affirmant détenir la vérité. Le Lean a vu le jour dans la région de Mikawa, où Sakichii Toyoda essayait de simplifier la vie de sa mère – une modification technique à la fois. Ce même processus a conduit à la célèbre innovation du Jidoka, qui a permis à la famille Toyoda de financer son entrée sur le marché automobile. Et si nous posions un nouveau regard sur le kaizen, en laissant pour une fois de côté notre perception occidentale et en essayant de le comprendre du point de vue de ses origines spécifiquement bouddhistes, confucianistes et taoïstes ?
Il est tentant de croire que le lean et le kaizen nous aideront à réparer nos systèmes qui sont dans un état de « bazar stable », mais surtout en bazar. Cependant, dans le bouddhisme, rien n'est stable, tout n'est que changement. Et devinez quoi, kaizen est synonyme de changement – pour le meilleur, espérons-le – mais il implique également suivi et appropriation. Il exige que nous sachions nous approprier le changement et le superviser pour nous assurer qu'il fonctionne dans le monde réel, avant de passer au changement suivant. Quant au taoïsme, il recherche la manière la plus simple de faire quelque chose en suivant les exemples de la nature. Il nous incite à nous interroger sur la manière dont nous pouvons assurer le suivi d'une manière simple et appropriée, sans fioritures, tandis que le confucianisme considère que pour faire les choses correctement, il faut adopter le bon comportement ou le bon rituel en fonction de la situation. Quel serait donc le bon rituel ou le bon comportement à adopter en matière de changements techniques et de suivi ? D'autre part, le management à l'occidentale, avec sa prédilection pour les fonctions et les silos, nous a appris que c'est aux cadres supérieurs qu'il incombe de définir et de décider le changement, aux cadres intermédiaires de le mettre en œuvre et au personnel de première ligne (et ça, on ne le dit jamais) d'en subir les conséquences. Le management « AFP » classique selon le nom qui lui a été donné chez Harley Davidson : Another Fine Program Encore un beau projet !
Une conversation informelle durant un dîner de gala à l'occasion d'une conférence avec un directeur d'usine Toyota nous a révélé quelque chose d'intéressant lorsque nous l'avons interrogé sur une chose que nous avions vue en visitant des usines Toyota au Japon. « Pourquoi y a-t-il tant de monde sur la ligne qui discutent avec les opérateurs ? » Nous savions que les ingénieurs du département technique se rendaient fréquemment sur la chaîne de production pour s'informer sur leur conception, mais nous n'avions pas réalisé à quel point il s'agissait d'une étape formelle impliquant des responsabilités clairement définies. Le directeur de l'usine nous a expliqué que l'ingénieur qui discute avec l'opérateur est probablement en train de vérifier une modification technique qu'il a apportée, et que c'est ce qu'on attend de lui. Cela signifie que, dans le cadre de l'approche kaizen du changement, l'ingénieur ou le directeur qui effectue le changement en est réellement propriétaire et qu'il est responsable de son bon fonctionnement pour le personnel sur le terrain – en veillant à ce que le travail des opérateurs devienne plus facile, et pas l’inverse – et en s'assurant que la qualité du produit (ou du service) s'améliore pour le client, et pas l’inverse. Il en va de même pour les modifications des processus de production ou les changements organisationnels. Il y a une responsabilité claire de définir le changement et de s'assurer qu'il fonctionne, pour le meilleur, et, par voie de conséquence, de développer à la fois l'entreprise et les personnes en synergie.
CONCLUSION
Nous sommes persuadés que le lean est avant tout une affaire de personnes, mais sans une responsabilité claire en matière d'ingénierie, l'intérêt porté aux personnes nous amènera à effectuer des changements dans tous les sens sans améliorer le système dans son ensemble. Quelle est donc la boussole qui nous guide pour effectuer les bons changements, ceux qui auront un impact sur la performance de notre entreprise ? C'est là que le lean devient stratégique et que notre approche de la stratégie change. Au lieu de laisser les employés faire face aux conséquences de nos changements, nous allons voir sur le terrain, pour observer les conséquences de nos changements et nous y confronter. Cela suppose d'accepter qu'il y a souvent une différence entre ce que nous imaginons et ce qui se passe en réalité. Observer et se confronter signifie accepter et corriger les conséquences de nos changements et reconnaître que les employés de première ligne ne devraient pas être abandonnés à eux-mêmes pour y faire face. Appropriez-vous les changements techniques et leur suivi, afin d'améliorer les choses pour les clients, les opérateurs et la planète !
Article de Eivind Reke, Cyril Gras et Daryl Powell paru dans Planet Lean.
Traduction de Marc-Antoine Guichard, Nicolas Villemain et François Lopez.
Téléchargez le PDF
Cet article L’art et la manière du kaizen est apparu en premier sur Institut Lean France.
A lire aussi
-
Une supply chain en juste-à-temps pour accélérer l’apprentissage
Publié le 03/11/2020
Nous revoilà en confinement – je souhaiterais avant tout partager une pensée...
-
La théorie de la transformation lean
Publié le 09/05/2022
Dans cet article théorique passionnant, l’auteur nous rappelle comment, dans une...
-
Comment avoir des standards quand il n’y a pas deux cas identiques dans des activités de services ?
Publié le 10/10/2019
Cher Gemba Coach, Je travaille dans le secteur des services, et j’ai des...
-
Le Management rechigne à aller sur le gemba
Publié le 29/06/2015
Cher Gemba coach, J’ai décidé d’emmener mon équipe de managers sur le gemba...
-
Lean et psychologie du changement
Publié le 12/11/2018
Cher Gemba Coach, Avez-vous une psychologie du changement ? Si oui, quelle est-elle?...
-
Publié le 05/03/2019
Cher Gemba Coach, Mon Sensei est devenu fou : il parle à nos pièces. Dans...
-
Commençons par arrêter le sabotage !
Publié le 01/10/2019
« Optimisez-moi les dépenses en marketing, » « il nous faut un programme de...
-
Il ne peut y avoir d’entreprise lean. Il n’y a que des penseurs lean, du PDG au concierge.
Publié le 23/10/2017
Lorsqu’on m’a enseigné le conseil, dans un grand cabinet à Londres il y a...
-
Publié le 08/01/2019
L’Obeya permet de réduire le nombre d’inconnues avant de partir sur le...
-
Publié le 04/02/2025
Cette question, apparemment banale, que posait souvent Freddy Ballé[1] – le...