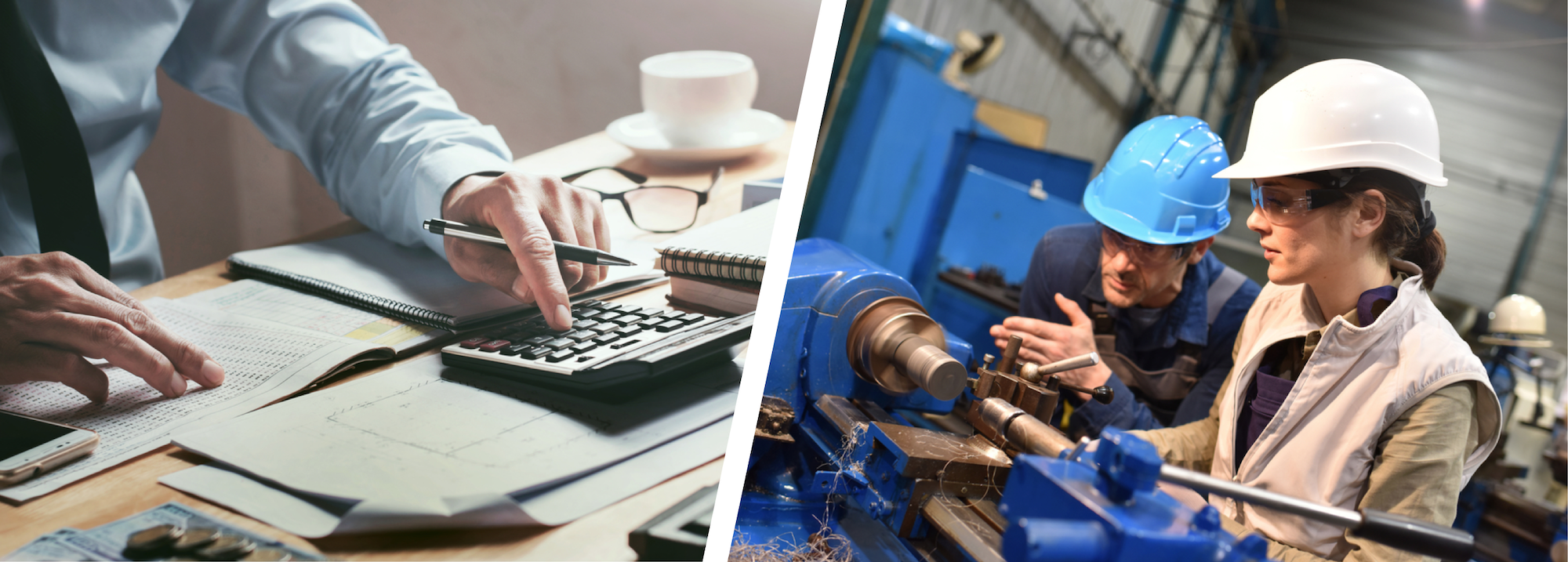
Avec la perte de PIB et de chiffre d’affaires que nous venons tous d’encaisser, personne ne le conteste, nous devons réduire notre base de coûts. Les financiers, tout comme les consultants en organisation, ne nous ont pas attendus : les tableurs sont en surchauffe depuis mars et les vieilles recettes éprouvées ressortent du placard.
En voici par exemple qui nous sont familières : repousser tout ce qui ne parait pas indispensable, par exemple les déplacements, la formation et les projets ; réduire la masse salariale, en commençant par l’intérim et les CDD, et geler tous les recrutements ; automatiser, pour remplacer les humains, susceptibles de contracter un virus, par des machines qui s’en moquent ; externaliser certains services non essentiels ; réorganiser l’entreprise de manière à créer des synergies et des gains de postes avec des services partagés ou des regroupements d’activités ; délocaliser des achats ou des productions dans des pays low-cost.
Ces recettes portent une promesse de réduction de coûts à court ou moyen terme mais c’est un jeu de dupes, pour 3 raisons principales :
1.Les coûts réels pour l’entreprise sont rarement mesurés et mesurables. On vend une réduction de coûts immédiate (un salaire roumain est moins cher qu’un salaire français) mais on ne mesure pas le coût de l’interface, de la résolution de problèmes et de la variabilité accrue sur une supply chain distendue. Une nième ré-organisation de l’entreprise peut donner l’illusion d’un second souffle, mais fondamentalement, toutes les énergies se mobiliseront bien plus sur les passations et suppressions de poste à grande échelle, la création de nouveaux réseaux internes et la mise à jour des rôles et responsabilités, que sur la valeur pour le client et le support à l’ensemble de la supply chain, seuls susceptibles de nous maintenir sur le marché et de tirer parti de la reprise.
2.Externaliser ou délocaliser la gestion d’une activité sont des décisions plus lourdes qu’on ne le pense : cela revient à dire qu’on renonce définitivement à apprendre et à développer un savoir-faire sur le domaine qu’on confie à un tiers. C’est rarement sans conséquences sur notre compétitivité future. La délocalisation de la recherche à Singapour ou du développement informatique en Inde se paiera cher, tôt ou tard.
3.Supprimer un poste, geler un projet, sursoir au plan de formation, automatiser, abandonner un fournisseur partenaire au profit d’un prestataire lointain, sont autant de coups de canif dans le contrat humain implicite qui nous lie les uns aux autres et qui nous fait avancer sur une vision d’entreprise ou de société.
Le coût induit de ces solutions toutes faites est bien souvent plus lourd que le gain qu’on nous en fait miroiter.
L’approche lean sur les coûts est fondamentalement différente. Elle passe par le kaizen de tous, partout, tout le temps. La réduction des coûts lean n’est pas une activité qui se pratique en batch, quand la crise est là et qu’on ne peut plus reculer. Elle se travaille avant, pendant et après, en partant de trois principes fondamentaux :
- Traiter chaque problème, dès qu’on le voit, sans attendre qu’on en ait suffisamment de même nature pour constituer une belle tête de pareto. Cela permet d’éliminer tous ces petits défauts qui à la longue usent ceux qui construisent, livrent ou utilisent le produit ou service. Chaque petit gain de temps et de matière contribue peu à peu à la construction de la productivité et de la valeur.
- Mettre au service de ce kaizen au quotidien l’ensemble des compétences qui peuvent aider, sous forme de chaine de support : les managers pour leur capacité à mobiliser du temps, du budget ou d’autres fonctions ; les experts, pour leur savoir-faire ; les autres membres de l’équipe pour leurs observations au quotidien, leurs idées et pour obtenir leur adhésion à la nouvelle approche.
- Le but de ce kaizen au quotidien est de nous faire découvrir ce que nous ne savons pas. Nous faire comprendre où sont nos erreurs de jugement, nos misconceptions (Taïchi Ohno dans Workplace management). Car ce sont ces misconceptions qui coûtent cher à l’entreprise, c’est là la vraie mine d’or de la réduction des coûts.
Les champs de réduction des coûts sont inépuisables du point de vue du lean :
- La mise à disposition du produit ou service en bon-du-premier-coup : temps perdu, attentes, remises ou pénalités versées en compensation d’un retard ou d’une mauvaise qualité, simplement parce que le bon-du-premier-coup n’a pas été travaillé à la livraison ! Le mieux est d’aller voir les réclamations clients très régulièrement, on y trouvera une belle source d’optimisation des coûts.
- Le geste, car d’un geste à l’autre, il peut y avoir des différences majeures en termes de rendement (des opérateurs aguerris sur des opérations complexes peuvent tenir un bon-du-premier-coup à 80% quand d’autres ne dépassent pas 25%). Il suffit pour s’en convaincre d’observer des sportifs qui pratiquent régulièrement leur geste et l’efficacité qu’ils en tirent par rapport à de simples amateurs.
- Le work content : peut-on réduire ce mouvement inutile qui prend du temps et qu’on fait 200 fois par jour ? Et qui finit par déboucher sur des TMS, des arrêts de travail et de la douleur humaine ?
- Les machines : une machine qu’il faut surveiller sans arrêt coûte cher. Comment la rendre autonome et capable de s’arrêter au premier défaut ou dès lors qu’une une condition de bon fonctionnement n’est pas confirmée ? Comment automatiser le chargement – déchargement des pièces ou données, qui est sans valeur ajoutée, pour libérer l’humain sur des tâches d’amélioration continue ? Comment la concevoir modulable pour la faire évoluer à peu de frais ? Et flexible pour assurer la production de plusieurs produits différents ? Comment, enfin, en augmenter la durée de vie ?
- Les composants : peut-on assurer le même niveau de fixation avec un boulon de moins ?
- Les rebuts ou déchets : comment perdre moins de matières, car ces rebuts ou déchets ont été achetés mais non vendus ? Comment recycler ou réutiliser les rebuts ? Ce champ de réflexion offre l’avantage supplémentaire, comme pour l’énergie, de protéger la planète.
- L’énergie : comment moins consommer d’eau, d’électricité ou d’autres ressources naturelles qui ne sont pas inépuisables ?
- Les emballages : combien d’air transporte-t-on dans nos cartons ? Nos emballages sont-ils ré-utilisables ?
- La supply chain : la gestion par petits lots, en juste-à-temps, est le plus sûr moyen de gagner en lead time, en stocks, en coûts de manutention et en m2. Où peut-on s’améliorer ?
- La conception des produits ou services : comment concevoir un produit ou un service en se fixant un target cost à ne pas dépasser ? A-t-on pris en compte la fin de vie du produit ? Quel coût pour la société représente sa fabrication, son transport et son usage ? Comment le réduire ? Et est-on en train de concevoir un produit qui nous plait ou un produit qui se vendra ?
- L’industrialisation des nouveaux produits ou services : les ingénieurs de développement sont-ils en train de travailler avec ceux qui fabriqueront ou livreront le produit ou service ? Prennent-ils en compte leurs contraintes ?
- Les projets : réfléchit-on suffisamment à l’impact qu’auront ces projets sur l’organisation ? Quelles perturbations sont à prévoir ? Raisonne-t-on vraiment à charge et à décharge sur chacun de ces projets ou nos biais cognitifs nous poussent-ils à n’en voir que les gains sans en avouer les inconvénients ?
Il ne s’agit pas de solutions globales, pré-digérées en autant de jalons par des consultants qui les vendent tous azimuts, mais de contre-mesures soigneusement réfléchies à des problématiques individuelles, localisées. Le lean ne cherche pas à trouver – 500 x 1 en 2020 mais - 0.5 x 100 tous les ans, tout le temps. Ce qui a le mérite d’ailleurs de générer en amont de la trésorerie qui s’avèrera indispensable en cas de crise, garantira l’autonomie par rapport aux instances financières, et permettra de maintenir le kaizen et l’emploi, même en cas de baisse du chiffre d’affaires.
Car nous vivrons d’autres crises, inévitablement, périodiquement, ne serait-ce qu’au travers de changements de modes de consommation inéluctables ou de l’arrivée de nouveaux concurrents hackant notre marché. Nous devons juste apprendre à réduire nos coûts intelligemment, en permanence, pour nous y préparer au mieux. Apprenons à distinguer la réduction de coûts lean, tout le temps, partout, avec l’aide de chacun, et qui recherche l’apprentissage et le développement du savoir-faire, du cost-cuttingcorporate aveugle, par lots, décidé en central. Nous avons assez souffert pendant le confinement de décisions centralisées prises en notre nom, pour notre bien et dont certaines, dans notre contexte, nous paraissaient totalement ubuesques. Reprenons la main et décentralisons la réduction de coûts !
Catherine Chabiron
Téléchargez cette newsletter en PDF
Cet article Oui, il faut réduire les coûts… mais pas n’importe comment ! est apparu en premier sur Institut Lean France.
A lire aussi
-
Lean et développement personnel
Publié le 06/03/2023
Les questions qu’on me pose le plus souvent sont « comment convaincre mon...
-
Bon et mauvais consultant lean ?
Publié le 04/08/2017
Si le Lean n’est pas une arnaque – même s’il existe des arnaqueurs –...
-
Comment faire du 5S quand tout le monde travaille différemment ?
Publié le 07/02/2020
Cher Gemba Coach,Comment mettre en œuvre le 5S dans notre petit atelier en pleine...
-
Le management visuel chez Toyota
Publié le 21/09/2018
Cher Gemba Coach, Nous avons déployé le Lean Visual Management dans mon entreprise...
-
Publié le 28/01/2019
Cher Gemba Coach Nos équipes ont de bons résultats avec le Kaizen, mais rien ne...
-
Qu’est-ce qu’une vraie transformation Lean ?
Publié le 19/08/2021
En s’intéressant aux transformations réussies, les auteurs expliquent pourquoi...
-
Le Management rechigne à aller sur le gemba
Publié le 29/06/2015
Cher Gemba coach, J’ai décidé d’emmener mon équipe de managers sur le gemba...
-
Des conseils pour appliquer le SMED dans un atelier d’emboutissage ?
Publié le 11/06/2019
Cher Gemba Coach, Nous avons appliqué le SMED pour accroître la flexibilité de...
-
Commencer par le takt time produit
Publié le 17/05/2024
En adoptant une perspective de takt time produit, nous pouvons mieux aligner les...
-
Pourquoi opposer encore et toujours qualité et rentabilité quand on a le Jidoka ?
Publié le 07/06/2019
Le monde de l’industrie fait l’objet d’un paradoxe : améliorer la...