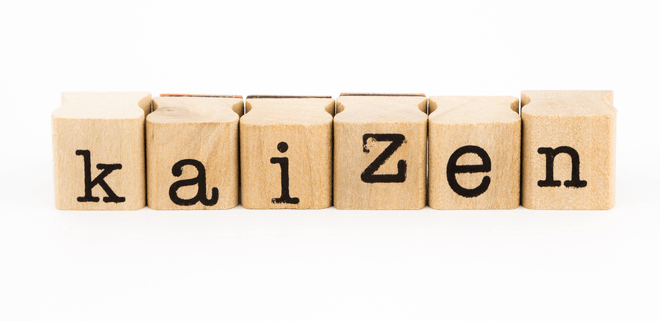
Traduction d’un « post » de Art Byrne (Auteur du formidable livre « Le virage Lean »). Titre original : « Kaizen Learning vs Traditional problem-solving » publié par The Lean post, le 10/12/2015.
Le Lean apporte une approche fondamentalement différente en matière de résolution de problèmes que la plupart des pratiques constatées dans les entreprises. C’est une méthode qui engage les gens sur le terrain à améliorer sans cesse leur travail pour « apprendre en faisant ». La plupart des entreprises délèguent les problèmes importants à des équipes d’experts spécialisés, qui prennent des mois pour établir un plan et encore plus longtemps pour obtenir des résultats pérennes. En général, les entreprises abordent la résolution de problème ou tout autre activité d’amélioration en constituant une équipe. Transversale par nature, elle sera constituée de membres des équipes support. Mais ces personnes très importantes sont toutes très occupées par leur travail quotidien. De ce fait, l’équipe va commencer par se fixer un agenda de réunions, une fois par semaine par exemple, pour réfléchir au problème qu’on leur a assigné. Au fur et à mesure du temps, deux ou trois personnes seront absentes de ces réunions car « trop occupées » ailleurs. Au démarrage du projet, les gens vont commencer à définir différentes approches ou solutions. Ces propositions entraineront un besoin de nouvelles données. Après plusieurs mois d’analyses intensives, l’équipe se mettra d’accord sur un plan. Il est important de noter qu’à ce stade, le seul « output » de l’équipe est juste un « plan ». Tout changement véritable est planifié pour le futur. D’abord, le plan doit être passé en revue et approuvé par un manger hiérarchique. Et rien ne sera donc réalisé à ce stade. L’aversion au risque est communément partagée dans les entreprises. Le Management veut être sûr que toute proposition de changement a une forte probabilité de réussir, et peut être aussi qu’elle est compatible avec la manière de faire habituelle. Très souvent, cela signifie que vous devrez respecter les desideratas des divers départements fonctionnels ou d’autres silos de ce genre, et ne marcher sur les pieds de personne !! Respecter cette approche dépassée, lente, et précautionneuse ne vous mènera pas très loin. En tout cas, cela ne vous permettra pas de réaliser rapidement des améliorations. Mais cette méthode de travail est tellement confortable que l’on comprend mieux les choix faits lors de leur « passage au Lean ».
Prenons le Six Sigma par exemple : de nombreuses entreprises choisissent cette approche pour s’engager dans le Lean. Ceci est, bien entendu mal avisé. Le Six Sigma est un des outils de la « boite à outils Lean », mais ce n’est pas du Lean. Ces compagnies choisissent le Six Sigma, car il est très proche de leur manière de faire habituelle. Et donc, pour elles, faire du Lean est juste « faire la même chose, un peu mieux ». Ce qui n’est pas Lean du tout !! Les entreprises traditionnelles qui utilisent le Six Sigma commenceront donc par sélectionner un groupe de techniciens et ingénieurs pour les former, pendant plusieurs mois, à l’usage des outils statistiques, base du Six Sigma. Une fois que vous avez formé le premier lot de « green belt » et « black belt », vous les faites travailler sur divers projets pendant 3 à 6 mois. Ils étudient, analysent et parfois résolvent des problèmes que vous leur avez soumis. C’est très bien, et cela génère aussi parfois des gains substantiels. Malheureusement, cette approche ne s’attaque qu’à environ 10 à 20 des gains réalisables ! Six Sigma permet de faire un pas sur les 20 pas possible, par exemple, mais cela n’affecte jamais la structure organisationnelle. Si ces 20 étapes se situent dans 20 différents silos fonctionnels, rien d’important ne change. Vous êtes heureux car vous avez une ribambelles de « green and black belt », mais vous avez toujours 6 semaines de Lead-Time !! Le statu quo est maintenu, vous avez quelques gains, sans inconfort ! Rien de vraiment radical… Une bonne opération pour les entreprises classiques qui veulent faire de l’amélioration en restant dans leur zone de confort. Le problème, c’est que vous pilotez un business, pas un cours de karaté !!
Adopter une pratique Lean basé sur l’approche Kaizen « apprendre en faisant » est radicalement différent : c’est une activité ou l’on « fait », au contraire de « planifier », tel que décrit plus haut. Une machine que vous n’avez pas bougé depuis son installation 10 ou 15 ans auparavant, sera déplacée dans l’après-midi ou au pire dans la journée ! Vous obtiendrez des résultats tangibles en moins d’une semaine. J’ai vu ça tellement de fois !! La raison principale est que l’équipe est affectée au kaizen à plein temps ! Cet effort, court et intense, focalise chaque personne sur un objectif précis dans un minimum de temps, une approche qui distingue radicalement le kaizen de toute autre méthode de résolution de problème, et qui le rend si puissant. Alors que l’équipe traditionnelle n’a pas encore fait sa deuxième réunion, l’équipe Kaizen a déjà obtenu des améliorations significatives. Vous avez des solutions, pas des plans !! Mais il y a bien plus que ça : d’abord l’équipe kaizen comprend des opérateurs et des supports (pas seulement des supports comme décrit ci-dessus), ce qui signifie que les gens qui font le travail, améliorent le travail, avec les leaders de leur atelier. Ce qui donne à l'équipe l’occasion d’apprendre tout au long de l’exercice. L’équipe comprend aussi des gens, comme la maintenance ou l’informatique, qui peuvent traiter des problèmes techniques sur le tas. Comme les gens du terrain sont présents, les meilleures idées sont en général produites. Et de plus cela donne l’assurance que les améliorations seront approuvées par ceux qui les appliqueront. Cela donne enfin la possibilité aux participants de se sentir engagés et de voir que les changements positifs peuvent finalement arriver !!
Commentaire de Mark Graban, un ancien de Toyota US : « je ne suis pas sur que Six Sigma fasse partie de la Boite à Outils Lean » ; en tout cas c’est très optionnel ; Toyota ne l’utilise pas, simplement des outils statistiques pour résoudre des problèmes qualité. »
Le commentaire personnel de Richard Kaminski : Les kaizen events dont parle Art Byrne sont bien entendus des outils très puissants. Mais ils ne doivent pas occulter le fait que le Kaizen, « tous les jours, tout le monde » est le coeur de la pensée Lean. De cette manière on évitera la pratique courante qui consiste à ne faire que des kaizen évents (appelé en France « Hoshin ») alors que l’amélioration continue, avec des petites actions, individuelles ou collectives, sur une foule de petits problèmes quotidiens, et débouchant sur de nouveaux standards, est la pratique Lean de base.
Cet article Le Kaizen, un outil de développement ! est apparu en premier sur Institut Lean France.
A lire aussi
-
Lean et démarrage de production
Publié le 09/01/2020
Cher Gemba Coach, Le Lean peut-il aider un démarrage de production ? Le Lean,...
-
Un terrain de jeu pour un travail d’équipe lean et collaboratif
Publié le 20/11/2018
Encourager ses employés à penser de manière autonome aux problèmes et à...
-
Comment puis-je utiliser une Obeya pour apprendre plutôt que pour du pilotage de projet?
Publié le 15/10/2015
Excellente question – en effet, la plupart des obeyas que je vois sont organisées...
-
Immersion dans une entreprise Lean du monde numérique – Chapitre 5
Publié le 05/11/2021
Depuis maintenant quelques années, Theodo a fait de la qualité et de la...
-
Publié le 09/09/2021
Les vacances sont l’occasion de ressortir les ouvrages mis de côté pour les...
-
Deux questions, deux trajectoires
Publié le 03/09/2024
« Vous avez fait ce que vous aviez à faire ? Montrez-moi vos indicateurs...
-
Les changements radicaux se construisent à petits pas sur le terrain
Publié le 04/05/2021
“Client en premier, commercial en second et production en troisième” : l’un...
-
Publié le 17/08/2018
Cher Gemba coach, Qu’en est-il du lean dans le digital ? Des idées ? Et sur...
-
Pourquoi se référer à Toyota ?
Publié le 01/05/2018
Je m’intéresse beaucoup au lean, mais je n’arrive pas à comprendre pourquoi...
-
Pourquoi les gens n’apprennent-ils pas ?
Publié le 17/11/2017
Cher Gemba Coach, Sur le Gemba, nous avons beaucoup de difficultés à manager le...