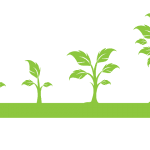
Le 16 octobre 1846, au « Massachusetts General Hospital » -sur lequel, sans le vouloir, depuis mon bureau du LEI, j’ai une vue directe, sur la rive opposée du Charles River, le docteur Henry Bigelow a exécuté la première opération au monde sous anesthésie (utilisant l'éther). Ses découvertes - qui ont permis, pour la première fois de l’histoire, de pratiquer des opérations chirurgicales sans aucune douleur pour les patients - ont été publiées dans un journal scientifique en novembre 1846 et avant juin 1847. Les chirurgiens utilisèrent alors l’éther dans le monde entier. Une idée rapidement diffusée.
Par contre, le chirurgien d'Édimbourg, Joseph Lister, a découvert dans les années 1860 que l'utilisation d'un désinfectant (l'acide phénique) sur les instruments, sur les sutures, sur les mains du chirurgien et sur leur tenue, complété par une bonne pulvérisation d'acide phénique sur le champ opératoire, réduisait très sensiblement le taux d'infection chirurgicale, (qui à cette époque était la cause de mortalité de la moitié des patients subissant des interventions chirurgicales lourdes). Il publia ses résultats en 1867 mais rien ne changeât dans les années qui suivirent. Il fallut plus de 30 ans pour que les idées de Lister soient généralisées et adoptées par les chirurgiens du monde entier. Une idée à diffusion lente.
L’excellent article d'Atul Gawande, "Slow Ideas", publié sur « The New-Yorker » du 29 juillet 2013, vous éclairera sur le sujet et je vous recommande vivement de le lire. Gawande conclut que la différence dans l'acceptation de ces idées était que l’anesthésie pouvait être administré avec des résultats rapides, sans gêne pour le chirurgien et avec un grand confort pour le patient alors que l’antisepsie exigeait des chirurgiens une réorganisation complète de leur activité et ralentissait leur « productivité » (Nombre d’interventions par unité de temps). Ceci causé par le changement de leurs instruments, de leurs tenues de bloc opératoire, et par le lavage des mains ( !) après chaque intervention. La plupart d’entre eux ne croyaient pas que leurs pratiques pouvaient être à l’origine des infections puisque elles apparaissent quelques jours après l’intervention chirurgicale. Pour que les méthodes de Lister soient acceptées par les chirurgiens, il durent changer leur propre image et passer du « charcutier » déterminé habillé de blouses de caoutchouc sombre, faisant au mieux ce qu’ils devaient faire dans un environnement mal organisé, au scientifique en blouse blanche essayant systématiquement de nouvelles méthodes en mesurant les résultats.
Nous avons été témoin de quelque chose de semblable avec la diffusion des pratiques Lean. La plupart des outils de la « boîte à outils » Lean : -
5S, implantation de cellule en flux pièce par pièce, production au temps takt, systèmes de flux tirés, ateliers d'amélioration éclair (kaizen blitz) - ont été entièrement développés avant les années 1960 chez Toyota au Japon et ont été mondialement déployés à l'extérieur de Toyota avec les chantiers kaizen à la fin des les années 1970. C’est encore un cas de diffusion d’idée lente comparée à l’anesthésie. Mais les méthodes de management Lean -
notamment le Hoshin Kanri (Déploiement de la politique) permettant au préalable de se mettre d’accord sur les stratégies et problèmes primordiaux à traiter, le rapport A3 permettant de traiter les problèmes importants, et un rigoureux système de mangement au quotidien pour stabiliser chaque processus créateur de valeur afin que les initiatives Kaizen puissent être conduites – ont été développées par Toyota avant le milieu des années 1960 .et sont seulement maintenant, 50 ans après, largement appliquées avec un succès confirmé. Un cas de diffusion d’idée très lent, même comparé aux contremesures appliquées par Lister au risque infectieux.
Dans le cas du Lean, la situation a, en réalité, été plus compliquée parce que les outils Lean et le mangement Lean sont liés – contrairement à l’anesthésie et la stérilisation.
Nous savons maintenant que la diffusion rapide des outils Lean ne produit pas des résultats durables sans le contexte organisationnel créé par le management Lean, qui est lui, lentement diffusé. Il n’est donc guère étonnant que beaucoup, dans notre communauté Lean, ressentent une frustration quant au progrès réalisés. Pour réfléchir de manière créative sur ce problème, nous devons commencer par nous demander quels sont les facteurs déterminants – (facilités ou difficultés) – de diffusion des idées dans une organisation. En général, nous savons que les idées qui ne perturbent pas la structure organisationnelle ou les routines, qui exigent peu de mise en pratique pour être maitrisées (ex : nouvelles technologies qui ne demandent qu’un branchement pour fonctionner), qui peuvent être mis en œuvre par des experts (Appel à consultants) et qui, sous les yeux des responsables de production, produisent des résultats spectaculaires et instantanés, sont relativement faciles à diffuser. Les chantiers Kaizen intensifs –. Le fameux chantier éclair qui durent 4 à 5 jours- conduits par des experts et produisant un retour sur investissement instantané autant sur les efforts du team que sur le plan financier en est un parfait exemple.
Par contre, les idées qui exigent une refonte des organisations, qui nécessitent de la pratique pour être maitrisées, qui doivent être mise en œuvre et soutenues par les mangers de proximité déjà surchargés par de constantes perturbations et qui ont obtenu des résultats seulement après des longues périodes d’efforts, seront vraisemblablement dures et lentes à faire accepter.
Le management Lean qui exige que les directeurs non seulement changent leurs méthodes, mais changent également leur approche intellectuelle sur la manière de gérer au quotidien (ex, Donner des ordres et mesurer les résultats au travers des indicateurs de performances clés – KPI- au lieu poser des questions et permettre aux collaborateurs de mieux réussir en en levant les barrières hiérarchiques) n’est surement pas le concept le plus dur à diffuser mais certainement beaucoup plus dur à mettre en œuvre. D’où une progression stable mais très lente. Que pouvons-nous faire avec cette perception de la situation ? Comment pouvons-nous changer notre pensée pour augmenter la vitesse de diffusion de nos idées ?
Premièrement, nous pouvons sortir du déni en admettant que les outils Lean seuls ne peuvent pas produire des résultats pérennes. J’ai récemment été témoin d’un exemple très significatif sur le changement d’état d’esprit dans une entreprise où j’ai accompagné le PDG sur un Gemba Walk pour prendre connaissance des résultats d’une vaste campagne de Kaizen conçue et menée par des consultants et accompagnée par un important groupe interne à l’entreprise, « d’excellence opérationnelle ». Au long du parcours, il est devenu évident que les opérateurs étaient prêts à travailler suivant les nouvelles méthodes, mais que le système de gestion courant ne facilitait pas la mise en pratique. Les signes de régression était clairement évidents, aussi bien par ce qui était visible que sur les tableaux de production journaliers.
A la question du PDG qui demandait au leader du groupe d’excellence opérationnelle interne ce dont il avait besoin pour améliorer la tendance, celui ci répondit qu’il était nécessaire d’augmenter de façon significative le nombre de chantier kaizen. Il posa alors un question sur le changement de l’approche intellectuelle: Ne faisons nous pas simplement – et ne refaisons nous pas- des chantiers dans une certaine confusion? Et si il en est ainsi pourquoi attendrions nous de meilleurs résultats avec plus de chantier Kaizen ? Après une longue pause, un des responsable de production suggéra que le temps serait mieux employé si l’on commençait par stabiliser les processus (dans lequel il venait juste de s’engager) au travers d’un management rigoureux au quotidien avant de lancer plus de chantier Kaizen. Le PDG conclut la discussion en leur demandant comment ils pourraient conduire une expérimentation sur l’hypothèse d’un management plus rigoureux au quotidien qui permettra de faire un Kaizen plus fructueux. Je souhaite de continuer encore longtemps la pratique des gemba walk avec un tel de résultat.
Deuxièmement, nous devons repenser le rôle des consultants Lean, internes et externes. Remontons à Frederick Taylor et à l’OST (Organisation scientifique du travail). Il a eu la conviction que l’amélioration des processus devait être réalisé pour les opérateurs créant la valeur ajoutée par des experts internes voire des consultants ayant, à priori, un savoir supérieur et sans avoir vraiment recourt aux managers. D’où le grand intérêt porté pour « l’excellence opérationnelle » ces dernières années. Il découle de cela deux types d’attitudes : Les managers de proximité sont dans une posture qui leur font penser qu’ils ne sont pas en mesure, par eux même, d’améliorer les processus en y entrainant les équipes, et même s’ils se sentent en capacité de le faire, ils ne le feront pas par manque de temps. Ils consacrent leur journée à gérer les perturbations créées par l’instabilité des processus. On peut donc comprendre qu’ils préfèrent avoir recourt aux experts internes ou aux consultants pour traiter leurs problèmes. A la grande satisfaction des ses derniers qui ont compris qu’une situation d’instabilité des processus sont sources de chantiers Kaizen à répétition et donc de business assuré.
D’après mon expérience, le rôle le plus profitable des consultants est d’aider les managers de proximité à établir des processus stables par un management rigoureux au quotidien. Plus, ils devraient entreprendre ces travaux avant de se concentrer sur l’aide à apporter aux managers de proximité pour améliorer les processus en vigueur. Cette voie amène vers des résultats à plus long terme, mais produit des processus stables qui permettront aux managers de proximité de bâtir une dynamique d’amélioration continue à long termeTroisièmement, nous devons arrêter de penser qu’un système de management Lean peut être mis en place dans les mêmes délais que les outils Lean par des activités Kaizen – autrement dit comme n’importe quel projet/programme rapide. Ceci a cause des nouvelles méthodes de management et de changement d’état d’esprit qui demandent des coachings fréquents (De par mon expérience de manager…. de coachings réguliers et nombreux) afin que les reflexes cognitifs changent. Ainsi le coaching des managers doit être une pratique continue et non un événement ponctuel. En conséquence de quoi, les top-managers doivent s’armer de patience, en posant des questions sur le processus de coaching des managers intermédiaires et de proximité plutôt que de se focaliser sur les résultats immédiats d’améliorations.
Quatrièmement, nous devons nous arrêter de nous décourager en répétant avec obsession que nous - PDG, consultants internes, directeur de production, rédacteur/chroniqueur sur le Lean - ne savons pas exactement comment introduire le management Lean dans nos organisations et qu’il n’y a pas assez de Senseï indépendants en capacité de nous l’enseigner. L’activité qui est la plus fondamentale – en fait le but essentiel de la pensée Lean – est de conduire des expérimentations (Méthode PDCA). Nous les utilisons couramment sur les processus à valeur ajouté. Nombre d’entre nous font cela chaque semaine. Maintenant il nous faut utiliser la méthode sur les processus de management en essayant des options différentes et également par le coaching. Il est nécessaire d’appréhender la situation actuelle de nos processus de management (en particulier en créant les fondements de la stabilité, base de Kaizen durable), essayer de nouvelles méthodes de management, déterminer quelles actions pourront stabiliser les processus et permettront une amélioration robuste, partager les idées pour s’adapter et proposer des méthodes innovantes, et de manière délibérée, observer systématiquement avec tout le monde les succès et les contretemps.
Les bonnes nouvelles : A la vu de ces principes, si nous pouvons agir comme la Communauté Lean peut le faire, je suis confiant que la diffusion des idées Lean avancera telle la diffusion des effets de l’éther et moins comme la diffusion lente des effets de l’acide phénique.
Titre original : YOKOTEN
[1] DE JIM WOMACK : Making Slow Ideas Go Faster, par: Jim Womack
, , (26/07/2016) Fondateur et conseiller principal du Lean Enterprise Institute.[1] Yokoten : terme japonais décrivant le déploiement des concepts, des idées, ou des politiques horizontalement au travers de l’entreprise.
Traduit par : Alain Coupeté. Téléchargez ici le pdfCet article Accélérer la diffusion des idées.. est apparu en premier sur Institut Lean France.